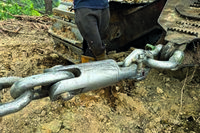
With the increasing use of tethered machines to replace fallers on slopes, on occasion well beyond the original limits of ‘traction assist’, there is high wear and failure at the connection of the shackle/s, wire rope/s or chain/s within the first ten metres from the machine.
While some failures can be identified as ‘mechanical damage’ due to the ropes and chains being picked up by the machine grapple or being worn by dragging over rock faces, or even by rubbing against the counterweight as the machines rotate, there are events which are classified as ‘normal wear and tear’ that may be premature failures.
The tether connections to the downhill machine are made with bow shackles on both single and twin rope winch systems. For Timbermax, Climbmax, Falcon and some early designs which use a single rope system, one set of unlubricated bow shackles is used. For double rope systems there are two versions of the tether connection to the downhill machine – unlubricated bow shackles used by EMS and lubricated twin pivoting clevises as manufactured by Lars Rosewarne with his ROB system, RWFS in Rotorua, and AP Hydraulics and Red Stag Engineering in Gisborne.
Bow shackle system
The bow shackle is the most commonly used connection in New Zealand, probably because of the familiarity with bow shackle use on hauler towers, swing yarders and trailer winches. Guildford Engineering Consultants, involved in the design and certification of tether winch systems and downhill machine tether connections used in North Island forests since 2005, believes that they are a source of fatigue when used in unlubricated tether connections which could result in premature or potentially catastrophic failure.
Reports from both New Zealand and the USA which measure the loads in the tether ropes, show that the line tension on the rope/s is more or less constant when the machines are cutting or placing logs but show spikes when the machines are moving. The explanation by the authors of these reports is that the machines jerk when moving (see graph to left).
We contend that the spikes are caused by the jerking which takes place when the two bow shackles slide over one another as the machines move up and down or side to side. The jerking is caused by friction welding. The normal process used in friction welding is when two pieces of metal to be joined are slid or rotated against each other at speeds of 75-110 metres per minute, with moderate joining pressures of 55-135 MPa. With the double bow shackles each having inner curved profiles while the sliding speed is low, assuming 10-tonne load and a 1-2mm square contact area, the contact pressure can be as high as 45,000 MPa. More than enough for minute friction welding to occur.
The peak loads shown in this load trace show loads fluctuating between five tonnes and 20 tonnes or a 381 MPa stress range, which on a nominal 22mm diameter shackle pin or 7/8 inch double wire or the 1 1/8 inch...